Leading Advantages of Dependable Welding Inspection Milwaukee in Construction
A Detailed List for Effective Welding Evaluation Practices
In the world of welding, the stability of structures is vital, necessitating an extensive technique to evaluation methods. A thorough list acts as a crucial tool in ensuring adherence to industry requirements, incorporating essential pre-welding, in-process, and post-welding analyses. By methodically dealing with product verification, weld quality, and complete paperwork, companies can significantly improve safety and efficiency. What certain components should be focused on in each stage to accomplish optimum outcomes? Checking out these vital components can produce understandings that greatly impact welding operations.
Comprehending Welding Standards
Welding requirements play an important role in making sure the top quality and safety of welded elements and structures. These criteria develop the standards for materials, procedures, screening, and examination, thereby supplying a structure for regular top quality assurance in welding procedures. Numerous organizations, including the American Welding Society (AWS), the International Company for Standardization (ISO), and the American Culture of Mechanical Engineers (ASME), have developed detailed criteria that govern different aspects of welding.
Recognizing welding criteria is vital for experts in the field, as adherence to these standards lessens the risk of flaws and failures in welded joints. These standards cover certain demands for weld top quality, consisting of appropriate tolerances, the kind of welding strategies to be used, and the credentials needed for welders and assessors.
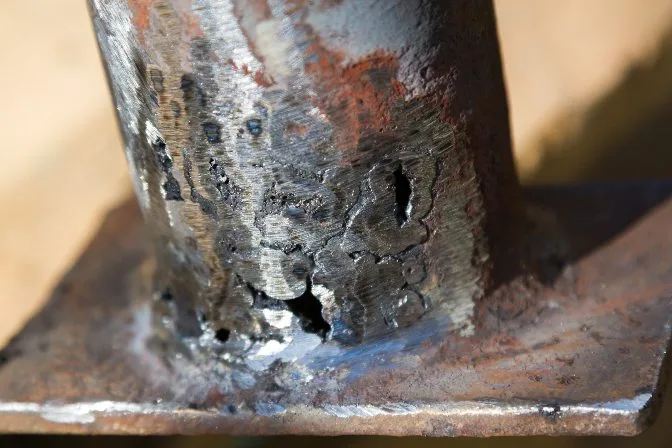
Pre-Welding Inspection Steps
Prior to any type of welding process starts, a thorough pre-welding inspection is necessary to determine prospective issues that might jeopardize the top quality of the weld. This preliminary step works as an essential foundation for making certain conformity with suitable welding codes and requirements.
The very first step in the pre-welding inspection is to confirm the products being used. This includes checking for the proper kind and grade of steels as defined in the task documentation. Next, it is important to evaluate the fit-up of the elements to make certain correct placement and joint configuration. Imbalance can lead to insufficient penetration and architectural weaknesses.
In addition, assessing the sanitation of the surface areas is essential; pollutants such as paint, corrosion, or oil can adversely influence the top quality of the weld. Following this, a complete analysis of the welding tools need to be conducted, making certain that it is calibrated and in great functioning condition.
Last but not least, reviewing the certifications of the welding workers is necessary. Welders need to have the required qualifications and experience to perform the details welds needed for the job. By sticking to these pre-welding evaluation steps, the possibility of defects and failings in the final weld can be considerably reduced.
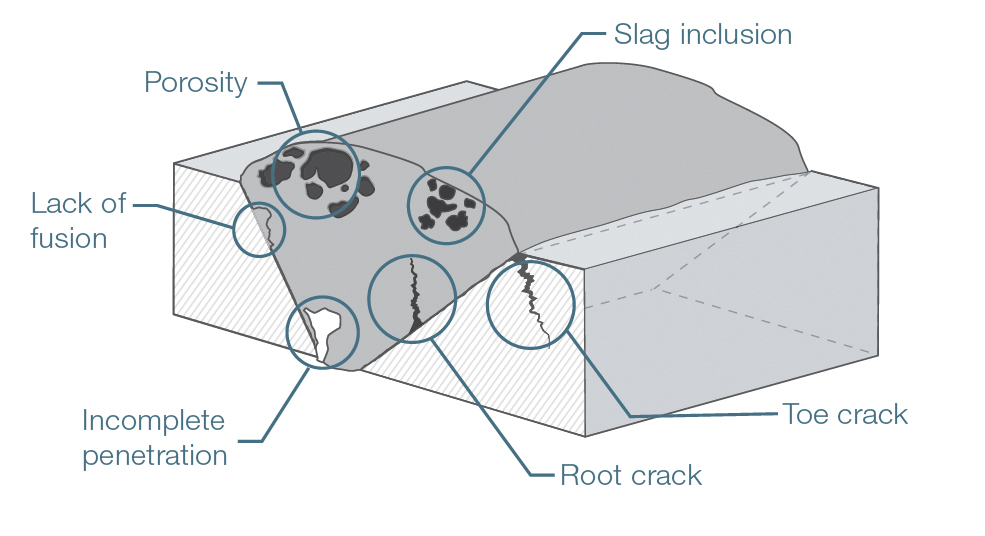
In-Process Assessment Methods
In-process inspection methods play an essential function in making sure the stability and quality of welds as they are being carried out. These techniques enable inspectors to identify flaws or inconsistencies from requirements in actual time, therefore protecting against costly repair work and guaranteeing adherence to design needs.
One key technique entails aesthetic examination, where inspectors assess the weld grain for uniformity, infiltration, and correct profile. This can be matched by the usage of evaluates to measure weld dimensions, making sure conformity with established tolerances. In addition, the application of non-destructive testing (NDT) approaches, such as ultrasonic screening or magnetic fragment testing, during the welding process can expose weblink subsurface imperfections that might not show up externally.
One more vital facet is checking welding parameters, consisting of voltage, amperage, and travel rate. Consistency in these parameters is critical for attaining optimum weld top quality. Documenting these parameters during the welding procedure provides a traceable record for future recommendation.
Educating workers in correct inspection techniques and the usage of proper devices improves the efficiency of in-process inspections. By incorporating these techniques, organizations can attain higher high quality welds, decrease rework, and eventually make sure the safety and security and dependability of bonded structures.
Post-Welding High Quality Checks
Complying with the conclusion of welding procedures, post-welding quality checks are important to verify that the welds fulfill all defined needs and standards. These checks are vital for making certain the honesty and resilience of the welded joints. The inspection process usually starts with an aesthetic assessment, assessing for surface area problems such as splits, porosity, or insufficient blend.
Ultimately, non-destructive testing (NDT) methods, such as ultrasonic screening, radiographic testing, or magnetic bit screening, may be employed to identify internal defects that are not visible to the naked eye. Each approach has its one-of-a-kind benefits and is picked based upon the weld's area, product my sources type, and the nature of the application.
Analyzing the mechanical residential properties of the weld, consisting of tensile stamina and ductility, can supply more guarantee of efficiency under functional problems. Overall, complete post-welding assessments are vital for maintaining adherence, efficiency, and safety and security to regulative and industry requirements.
Documentation and Reporting
Exactly how can effective documentation and reporting boost the welding evaluation process? Accurate documents and thorough coverage are essential elements that guarantee the honesty and high quality of welding operations. Welding Inspection Milwaukee. They function as a formal document of evaluation findings, facilitating accountability and traceability in conformity with market requirements

A well-structured coverage system makes it possible for assessors to clearly interact any type of non-conformances, disparities, or locations needing enhancement. This transparency cultivates a setting of continuous enhancement, as stakeholders can easily assess previous efficiency and carry out rehabilitative actions.
Additionally, effective documents consists of in-depth documents such as welding procedure specs (WPS), welder qualifications, and examination lists. These elements supply a framework for examining weld quality and adherence to developed standards. In case of disputes or quality issues, comprehensive paperwork acts as a trusted recommendation, reducing ambiguity and safeguarding all events entailed.
Last but not least, preserving arranged records helps in training and licensing employees, see post making sure that industry best practices are upheld. Eventually, precise paperwork and reporting not just enhance the welding examination process however also add to the general safety and reliability of welded structures.
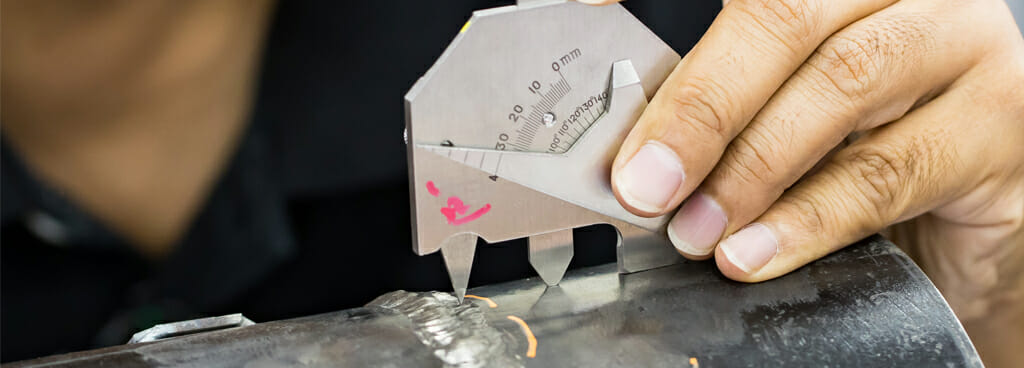
Final Thought
In final thought, a comprehensive list for reliable welding examination methods is crucial for guaranteeing high quality and safety in bonded structures. Adherence to established welding criteria, thorough pre-welding evaluations, rigorous in-process assessments, and comprehensive post-welding quality checks collectively contribute to the integrity of welded joints.
Welding requirements play a vital function in making certain the quality and safety of bonded frameworks and components. Numerous companies, consisting of the American Welding Culture (AWS), the International Organization for Standardization (ISO), and the American Society of Mechanical Designers (ASME), have established extensive standards that govern different facets of welding.
Adhering to the completion of welding procedures, post-welding top quality checks are important to validate that the welds fulfill all defined standards and requirements - Welding Inspection Milwaukee.In conclusion, a detailed list for effective welding examination practices is important for guaranteeing top quality and security in bonded frameworks. Adherence to developed welding criteria, careful pre-welding inspections, rigorous in-process assessments, and detailed post-welding high quality checks jointly contribute to the integrity of welded joints